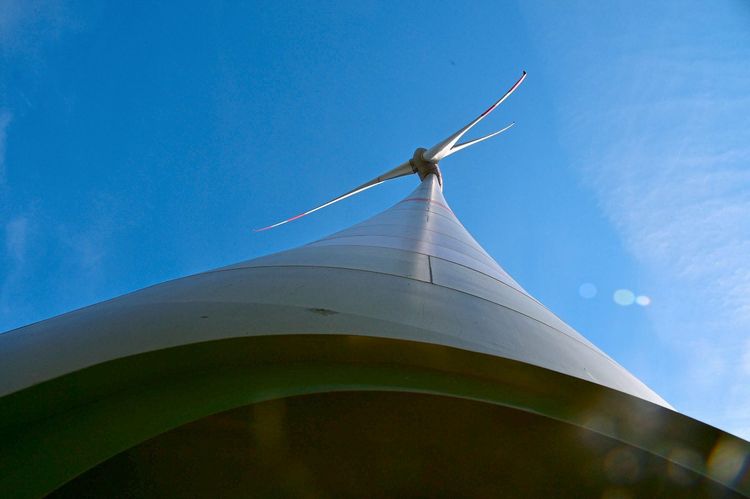
Ein wichtiger Bestandteil von modernen Windkraftanlagen – innen wie außen – sind Funktionslacke und Beschichtungen.
Der großflächige Einsatz von Sonnen- und Windstrom erhöht den Innovationsdruck, und das in vielerlei Sparten: Elektromotoren sollen kleiner und leistungsfähiger werden, um Autos pro Akkuladung länger rollen zu lassen. Generatoren und Rotorblätter von Windkraftanlagen sollen jahrzehntelang mit geringem Wartungsaufwand durchhalten. Transformatoren, Laderegler, Spannungswandler und natürlich auch Photovoltaikzellen müssen den Anforderungen von dezentraler Energiegewinnung und Elektromobilität genügen.
Materialwissenschaften, Leistungselektronik und intelligente Designprozesse sollen die Systeme effizienter machen. Dazu gehört auch eine Klasse von Werkstoffen, die man als Laie vielleicht nicht zuerst im Inneren eines Windkraftgenerators gesucht hätte – Funktionslacke. Sie machen aber viele der neuen Energietechnikdesigns überhaupt erst möglich.
Werkstoff-Weiterentwicklung
Sie trennen und isolieren Bauteile, schützen sie vor ungewollten Einflüssen und geben Stabilität, ohne aber erwünschte Interaktionen – etwa magnetische Felder – zu beeinträchtigen. Zum Teil sind die Werkstoffe Weiterentwicklungen von Technologien, die bisher beispielsweise in der Wasserkraft oder in der Luftfahrt eingesetzt wurden.
Hubert Culik ist Obmann des Fachverbands der Chemischen Industrie Österreichs, Präsident des Österreichischen Forschungsinstituts für Chemie und Technik (OFI), das auch im KMU-Forschungsnetzwerks Austrian Cooperative Research (ACR) vertreten ist, und Geschäftsführer des Unternehmens Rembrandtin Lack.
Er überblickt nahezu sechs Jahrzehnte der Entwicklung von Lacksystemen. "Als ich als Lehrling gestartet bin, haben wir Lack noch gekocht. Das waren Systeme aus Leinöl, die mit Harzen und Pigmenten modifiziert wurden – und zum großen Teil Bioprodukte", erinnert sich Culik. "Heute werden neue Lacksysteme dagegen mithilfe von statistischen Systemen in einer Entwicklungszeit von etwa drei Jahren entworfen."
Mit Backlack Pakete kleben
Einer der Funktionslacke, denen in der heutigen Energietechnik eine immer größere Rolle zukommt, sind sogenannte Backlacke. In Motoren und Generatoren kommen sie als Teil von Elektroblech zum Einsatz. Das sind Eisen-Silizium-Legierungen in Bandform, die Glüh-, Walz- und Lackierungsprozesse durchlaufen, um dann zu "Blechpaketen" verklebt zu werden. Aus ihnen werden Bauteile wie Rotor-, Stator- oder Trafokerne. In Culiks Unternehmen Rembrandtin ist die Windkraft ein wichtiger Einsatzbereich des Backlacks. Weitere Anwendungen der Technologie liegen etwa bei Magnetschwebebahnen oder bei Magneten im Teilchenbeschleuniger des Kernforschungszentrums Cern.
Die wichtigste Aufgabe von Backlack zwischen den einzelnen Stahllamellen ist seine isolierende Wirkung, die für eine Steigerung des Wirkungsgrads des Motors oder des Generators sorgt. Ohne sie würden die starken Magnetfelder Wirbelströme erzeugen und den Eisenkern aufheizen. "Heute sind die Backlackschichten zwischen den Lamellen gerade einmal zwei Mikrometer dünn, also ein Bruchteil eines menschlichen Haares. Dennoch isolieren sie perfekt und haben zusätzlich noch antikorrosive Wirkung, verhindern also ein Rosten", sagt Culik. Der Klebelack verhindert Vibrationen von Lamellen genauso wie das Eindringen von Wasser.
Sparsamer und haltbarer
Punkto Umweltverträglichkeit waren hier der Wegfall organischer Lösungsmittel und die Entwicklung wasserverdünnbarer Systeme in den letzten Jahrzehnten wichtige Schritte. Eine wesentliche Perspektive in der Entwicklung von Funktionslacken ist heute die Verminderung des Ressourceneinsatzes, betont Culik. "Die Strategie geht klar in Richtung von Systemen, die in ihrer Anwendung sparsamer und haltbarer sind. Eine Brücke wurde früher beispielsweise mit Lack in einer Schichtdicke von 400 Mikrometer überzogen. Heute ist man bei 150 und einer Haltbarkeit von mehreren Jahrzehnten.
Damit ist auch der Bedarf an Pigmenten, Harzen und Lösungsmitteln geringer." Ein anderer Aspekt ist die Verringerung des Energieaufwands bei der Fertigung selbst. "Prozesstemperaturen von 210 Grad, wie sie beim Trocknen von Metallbeschichtungen benötigt werden, sollen in Zukunft deutlich in Richtung 150 Grad gehen. Eine Möglichkeit ist hier, anstelle von Hitze mit UV-Strahlung zu trocknen."
Rotorbeschichtungen
Für die Lackentwickler ist nicht nur das Innenleben der Windkraftanlagen, sondern auch die Beschichtungen der Rotorblätter ein großes Thema. Die Oberflächen sind Wind, Regen und UV-Strahlung ausgesetzt. Dazu kommen die inneren Spannungen des Materials und Verformungen, die in den langen Rotorblättern entstehen. "Bei Flugzeugen hat man ähnliche Anforderungen.
Deshalb nutzt man in der Windkraft auch Verbundwerkstoffe und Spezialbeschichtungen, die in ähnlicher Form auch in der Luftfahrt zu finden sind", sagt Culik. Dazu kommen spezielle Schutzschichten an den Kanten, um die Stabilität zu erhöhen, und Eigenschaften, die etwa der Vereisung oder einer intensiven Reflexion von Sonnenlicht vorbeugen. Ein weiteres Beispiel für die Anwendung liegt im Photovoltaikbereich.
Eine spezielle Beschichtungstechnologie "mit Folienfunktion" ersetzt die Glasrückseite der Module, macht sie witterungsbeständig und spart Kosten. Sie sollen den Wirkungsgrad erhöhen, indem auch das rückseitig reflektierte Licht zur Energiegewinnung genutzt wird.
Zurück zu den Wurzeln
Derartige, auf spezielle Anforderungen getrimmte Funktionslacke werden heute mithilfe statistischer Methoden und chemischer Modellierungen, wie sie etwa in der Pharmaindustrie eingesetzt werden, gestaltet. Früher seien die Rezepturen und Formulierungen noch stärker als heute von individueller Erfahrung und von vielen Versuchsreihen abhängig gewesen, erinnert sich Culik. Aber auch heute dauert es noch an die drei Jahre, ein vollkommen neues Produkt zu entwickeln.
In einem Aspekt der modernen Lackentwicklung fühlt sich Culik allerdings wieder an die Zeit des Leinöls erinnert. "Blickt man auf die heutigen biobasierten Stoffe, hat man das Gefühl, es geht wieder zurück zu den Wurzeln. Es gibt bereits industrielle Prozesse, die Mais oder Cashewschalen nutzen", so der Experte. "Ein Produkt ist etwa Polyurethan-Lack mit einem Härter aus Maisstärke, das den petrochemischen Pendants mehr als ebenbürtig ist." Anwendungen gibt es etwa in der Fahrzeugindustrie. Culik: "Da gibt es durchaus Züge oder Autobusse, die bereits mit diesem Lack unterwegs sind." (Alois Pumhösel, 30.9.2020)