In der Oldtimerszene ist die Sache schon länger en vogue: Diverse Ersatzteile, bei denen sich die Anfertigung teurer Werkzeuge nicht lohnt, aufgrund von Stückzahl etwa, kommen schon seit Jahren aus dem 3D-Drucker. Mit kaum überbietbarem Interesse sehen sich aber auch die Autohersteller die Sache an, und jetzt ist es offenbar so weit, dass es in die Großserie gehen kann: Das Auto kommt aus dem Drucker.
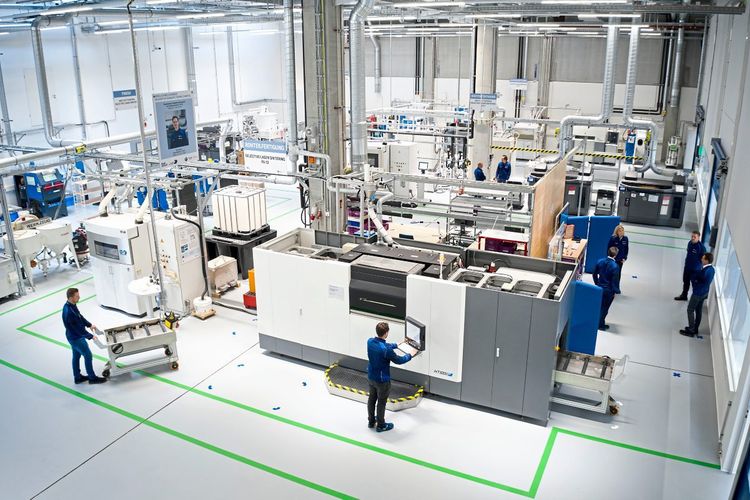
Das ist natürlich journalistische Verkürzung, so schnell geht es nicht, ein komplettes Fahrzeug aus der digitalen Welt in die analoge zu beamen, aber wie weit die revolutionäre Alternative zu den konventionellen Fertigungsmethoden bereits gediehen ist, zeigte jüngst BMW.
Der Konzern hat Ende Juni, in der Öffentlichkeit aufgrund der Corona-Krise eher unbeachtet, einen neuen Technologie-Campus für 3D-Druck eröffnet, an dem die Kompetenzen an einem Standort gebündelt werden. 15 Millionen Euro wurden investiert, der Campus vereint "die Produktion von Prototypen- und Serienbauteilen, die Forschung an neuen 3D-Drucktechnologien sowie die Qualifizierung von Mitarbeitern weltweit für den Einsatz der werkzeuglosen Verfahren unter einem Dach." Und klar, Bescheidenheit ist mitunter fehl am Platz, BMW konstatiert sich in der Autozunft die Technologieführerschaft beim Einsatz additiver Fertigungsverfahren.

Direkt neben den Kurfürsten
Bis zu 80 Mitarbeiter sind derzeit im neuen Kompetenzzentrum beschäftigt, 50 sündteure Metall- und Kunststoffanlagen bereits in Betrieb (mehr als 50 Anlagen finden sich zusätzlich an weiteren Standorten in aller Welt). Um im Konzern langfristig einen Produktionsausstoß von womöglich Millionen von Teilen zu erzielen, werde hier, so BMW, eine Fertigungslinie aufgebaut, die die gesamte Prozesskette abbilde – von der digitalen Produktionsvorbereitung über die Komponentenherstellung bis zur Nachbearbeitung.
Seit 2010 setzt BMW auf kunststoff- und metallbasierte Verfahren, für den Motorsport etwa. Die Entwicklung ist rasant: 2019 wurden bereits 300.000 3D-Teile hergestellt. Künftig sollen in Oberschleißheim, quasi in Nachbarschaft zur Sommerresidenz der bayerischen Kurfürsten – wo Manufaktur die dominante Fertigungstechnologie war, auch im Kutschenbau –, jährlich mindestens 50.000 Serienkomponenten sowie 10.000 Einzel- und Ersatzteile gefertigt werden. Damit, so BMW, stärke man die technologische Vorreiterrolle Deutschlands. (Andreas Stockinger, 12.12.2020)